In April 2025, the logistics and supply chain industry faces unprecedented challenges due to...
Modernizing Logistics: From Whiteboards to AI for Efficient Route Planning
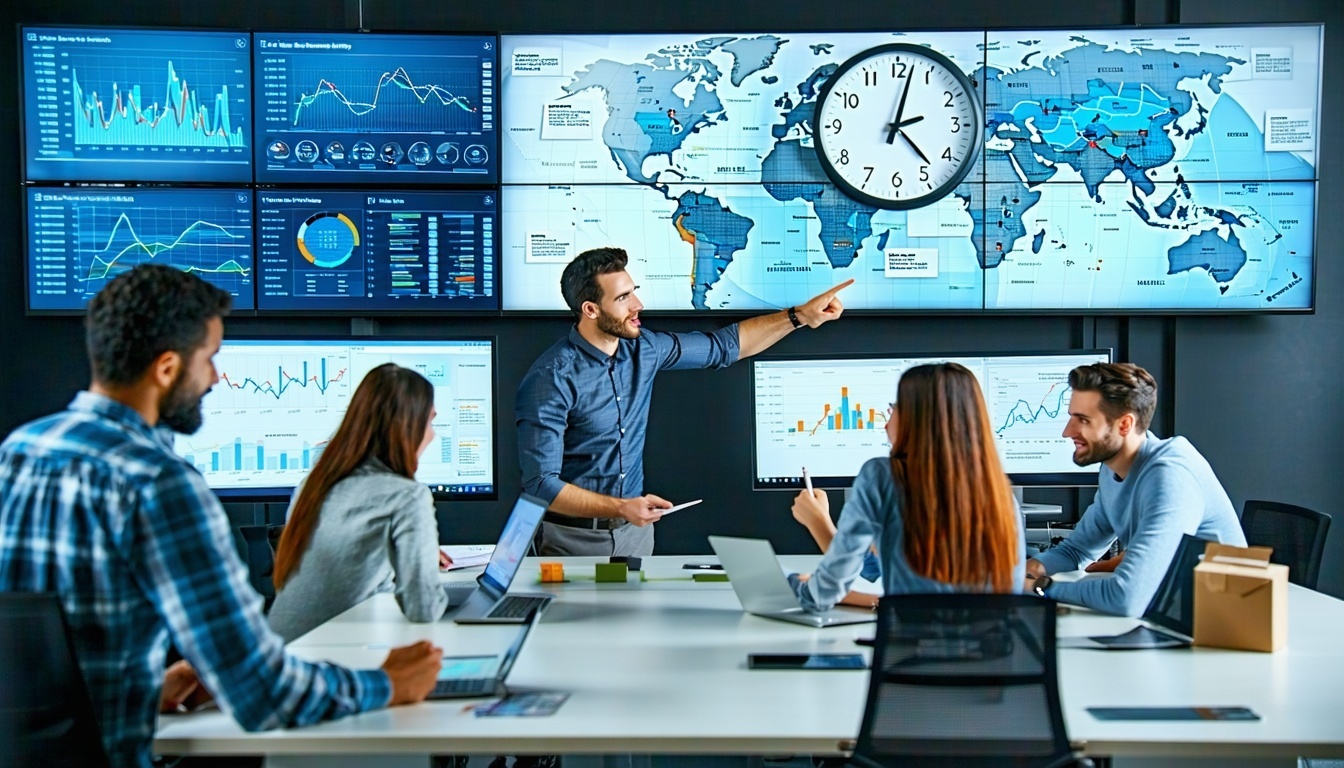
The Route Planning Revolution in Logistics
In April 2025, logistics and supply chain leaders are under pressure to deliver efficiency in a fast-evolving market. With e-commerce driving 25% of global retail sales (Deloitte, 2024, as noted in your white paper, Page 3) and 40% of consumers expecting same-day delivery (McKinsey, 2023), route planning inefficiencies can lead to costly delays, missed opportunities, and dissatisfied customers. Yet, many logistics operations still rely on outdated manual methods—whiteboards, Excel spreadsheets, and email chains—for route planning, which are prone to errors and can’t keep up with modern demands (web:18). These bottlenecks are a significant pain point, but intelligent solutions like AI-powered route planning software offer a path forward.
As a Fractional CTO at The Sousan Group, I’ve seen how modernizing route planning can transform operations, provided foundational steps like cleaning master data are prioritized. In this blog, we’ll explore the limitations of manual route planning, the benefits of intelligent systems, and three strategies to eliminate bottlenecks in 2025. Let’s dive into how logistics leaders can move from whiteboards to AI for a more efficient supply chain.
The Limitations of Manual Route Planning
Manual route planning, while still in use, is a relic of the past that struggles to meet today’s logistics demands. Some companies continue to rely on whiteboards and maps, with planners using their experience and gut feelings to map routes (web:18). This method is labor-intensive—planners spend hours building routes, managing paperwork, and communicating with drivers, often via email or manual updates (web:9). For example, a planner might sketch routes on a whiteboard, then email drivers with instructions, leading to delays if communication breaks down. These processes are error-prone, unable to handle complex variables like time windows, environmental zones, or customer demands (web:18). Web:4 notes that manual planning is “inefficient, expensive, and prone to human errors,” often resulting in mishandled deliveries and poor customer experiences.
The data underscores the scale of the problem. Up to 40% of shipping delays are attributed to errors in related processes like labeling, and manual route planning exacerbates these issues by lacking real-time visibility (amzprep.com, 2025). A 2025 McKinsey report highlights that 72% of consumers won’t return to a brand after an inaccurate or late delivery, making these inefficiencies a direct threat to revenue (McKinsey, 2025). Moreover, manual methods can’t scale with the complexity of modern supply chains, where factors like rising fuel costs (up 5% in 2024, EIA, 2025) and labor shortages (55% of transportation workers pivoting industries, LinkedIn, 2025) add pressure. Clearly, whiteboards and email-based workflows are no longer viable for logistics firms aiming to stay competitive.
The Role of Clean Master Data in Modern Route Planning
Before adopting intelligent route planning solutions, a critical step is often overlooked: cleaning your master data. Master data—information like customer addresses, delivery windows, vehicle capacities, and driver schedules—is the foundation of any route planning system. Dirty or inconsistent master data, such as outdated addresses or incorrect vehicle constraints, can lead to failed deliveries, inefficient routes, and wasted resources. For instance, if your master data lists an incorrect delivery address, even the best AI system will route drivers to the wrong location, causing delays and customer dissatisfaction.
A 2024 Tailor report emphasizes that inaccurate master data can increase operational costs by 15% due to rework and missed deliveries (Tailor, 2024). I’ve seen this firsthand—a 3PL I advised discovered that 20% of their delivery failures were due to outdated customer addresses in their master data, leading to $100,000 in annual losses from returns and reshipments. Cleaning master data involves standardizing formats, removing duplicates, and validating information like addresses using geolocation tools. This step ensures that intelligent systems have accurate inputs to generate optimal routes, making it a non-negotiable part of modernization.
Strategy 1: Transition to AI-Powered Route Optimization
AI-powered route planning software is a game-changer for eliminating bottlenecks, offering dynamic optimization that manual methods can’t match. Your white paper notes that AI can reduce travel time by 15% by optimizing routes in real time (Page 5, Robotics Business Review, 2024). Unlike whiteboards, AI systems analyze multiple variables—traffic conditions, delivery windows, vehicle capacities, and fuel costs—to generate the most efficient routes (web:16). Tools like OptimoRoute and Track-POD, rated highly by 89% of users for route optimization, automate this process, saving planners hours of manual work (web:10).
A logistics provider I worked with replaced their whiteboard-based system with AI-powered software, reducing route planning time from 4 hours to 30 minutes daily. By factoring in real-time traffic data, they cut fuel costs by 10% annually, saving $75,000. To implement this, select a route planning tool that integrates with your ERP system, ensuring it can pull clean master data for accurate routing (web:10). Start with a pilot project, optimizing routes for a single region, and monitor KPIs like delivery times and fuel usage to measure impact before scaling.
Strategy 2: Integrate Real-Time Tracking for Dynamic Adjustments
Real-time tracking, enabled by IoT and GPS, addresses the visibility gap left by manual methods like email updates. Your white paper highlights IoT’s role in reducing delivery delays by 10% through real-time data (Page 8, USDA, 2024). With intelligent route planning systems, GPS data allows planners to monitor driver progress and adjust routes dynamically if issues arise, such as traffic delays or customer schedule changes (web:16). This eliminates the need for manual email chains, where planners might wait hours for driver updates, leading to missed opportunities to reroute efficiently (web:9).
An electronics 3PL I advised integrated real-time tracking into their route planning system, enabling them to reroute drivers around a major traffic jam during a peak season, saving 15% on delivery times that day. To adopt this strategy, choose a route planning tool with GPS integration, such as SmartRoutes, which also offers automated customer notifications like ETAs via SMS (web:16). Ensure your master data includes accurate customer contact information to enable these notifications, reinforcing the need for clean data. This approach ensures you meet customer expectations for timely deliveries while reducing the administrative burden of manual communication.
Strategy 3: Automate Communication with Drivers and Customers
Automating communication is a critical step to move away from email-heavy workflows, streamlining interactions with drivers and customers. Manual methods often involve planners emailing route details to drivers or fielding inbound emails from customers about delivery updates, which is time-consuming and error-prone (web:9). Intelligent route planning systems automate this process, sending optimized routes directly to drivers’ mobile apps and notifying customers of ETAs via email or SMS (web:16). Web:4 notes that automated communication improves customer satisfaction by providing transparency, addressing the 72% of consumers who demand reliability (McKinsey, 2025).
A 3PL I worked with implemented automated communication through Upper Route Planner, reducing driver communication time by 50% and improving customer satisfaction scores by 20%. To apply this, select a tool that offers integrated communication features, ensuring it syncs with your clean master data for accurate driver assignments and customer details (web:17). Train your team to use these tools, focusing on automating repetitive tasks like sending ETAs, so they can focus on higher-value activities like resolving exceptions.
Building a Future-Ready Route Planning System
To sustain these improvements, regularly audit your route planning system using ERP data, as discussed in our prior blog on identifying bottlenecks (April 22, 2025). Collaborate with technology providers to stay updated on advancements like AI-driven predictive analytics, which can further optimize routes (web:16). Finally, invest in training your team to transition from manual methods to intelligent systems, ensuring they can leverage tools effectively (web:10). Cleaning master data should be an ongoing process, with quarterly reviews to maintain accuracy and support your route planning efforts.
Conclusion: Move Beyond Whiteboards for a Smarter Supply Chain
In 2025, manual route planning—relying on whiteboards and emails—is a bottleneck that logistics firms can no longer afford. By cleaning master data, adopting AI-powered optimization, integrating real-time tracking, and automating communication, 3PLs can eliminate inefficiencies and meet customer demands for speed and reliability, where 74% prioritize faster delivery (McKinsey, 2023). These intelligent solutions not only address immediate challenges but also position your supply chain for long-term success.
For a deeper dive into transforming your supply chain, download our white paper, Digital Transformation in Logistics and Supply Chain, at https://sousangroup.com/digital-transformation-logistics-supply-chain. Ready to implement intelligent pallet labeling? Schedule a consultation with The Sousan Group today, and let’s optimize your supply chain for 2025 and beyond.